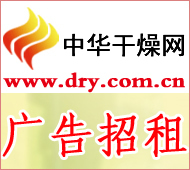
China Drying Network News With the development of the packaging industry, the demand for plastic products has risen rapidly, and the application of plastic films has been particularly extensive. As a single plastic film is difficult to meet the needs of flexible packaging, in practical use, multilayer composite films are more common. In the past, the production of composite membranes mostly used single-layer membrane dry or wet composite processes. However, due to the unstable quality, poor hygienic use of adhesives, and high cost, the product was gradually replaced by multilayer coextruded films.
Due to its low cost and good quality, multi-layer co-extruded composite films have become more widely used in China's food packaging and other fields. The market has also transitioned from three-tier to five-tier and seven-tier.
At the same time, the technical level of the domestic multi-layer co-extrusion blown film unit has been continuously improved. Although the key components such as the die need to be imported from abroad, the three-layer and five-layer production lines can basically meet the domestic needs and in some models. There are innovative designs.
Composite multilayer coextrusion process using multiple extruders, through a special extrusion head in a molten state material, forming a new functional thin film. A multi-layered, multi-functional composite film can be made by only one processing step, which avoids multi-pass production processes, reduces production energy consumption and material costs, produces no pollution in the production process, and has no residual solvent in the finished product. Other composite processes can save about 30% of production costs.
This film can be configured according to the user's requirements of different components to achieve different barrier requirements and cost requirements. The multi-layer co-extruded film has excellent barrier properties and high transparency, and can visually package the form and quality of the product. At present, the use of coextruded films in developed countries accounts for about 40% of the total packaging film.
Before the 1990s, China used rotary heads to produce two to three layers of co-extruded films. However, with the development of China's economy, the people’s living standards have been continuously improved, and the requirements for food hygiene and preservation have become more and more. High, three-layer packaging films gradually gave way to five or even seven films. Continuously catalyzing this process is the development of domestic multi-layer blown film equipment. At present, there are a number of equipment manufacturers represented by Shantou Jinming Plastic Equipment Co., Ltd. and Dalian Liaonan Donghua Plastic Machinery Co., Ltd. in China. They have been able to produce three-, five-, seven-, or even nine-layer coextruded film production equipment.
Domestic equipment is inferior to imported equipment in terms of product accuracy and reliability, but its price advantage is unmatched by the imported production line. It is because of excellent cost performance that domestic multi-layer composite membrane equipment accounts for half of the domestic market, and has greatly promoted the development and upgrading of multi-layer co-extruded composite membrane products in China.
Fast Dry Paper,Dry Sublimation Paper,Sublimation Fast Dry Paper,Fast Dry Transfer Paper For Sublimation
GREEN-LIFE PAPER LTD , https://www.sjgreenlife.com