We all know that the tool is the “teeth†of the machine tool, and the main factors that affect the cutting performance and tool life of the tool, in addition to the tool material, tool geometry parameters, tool structure, cutting amount optimization, etc., experience through a large number of tool edge passivation: A good edge type and edge passivation quality is also a prerequisite for the cutting tool.
The edge of the tool after sharp grinding by ordinary grinding wheel or diamond grinding wheel does exist microscopic notches of different degrees (ie, tiny chipping and sawing). The former can be observed with the naked eye and an ordinary magnifying glass, and the latter can be observed with a microscope with a magnification of 100 times (with 0.010mm). The microscopic gap is generally 0.01-0.05 mm, and the severe one is more than 0.1 mm. In the cutting process, the micro-notch of the cutting edge of the tool can be easily expanded to accelerate the tool wear and damage.
Modern high-speed cutting and automatic machine tools have imposed higher requirements on tool performance and stability. In particular, coating tools must be passivated before the coating to ensure the firmness and service life of the coating. The tool used in CNC machine tools and production lines imported from abroad has been completely passivated. There is a lot of information that the tool blade passivation can effectively extend the tool life by 200% or more, greatly reducing the tool cost, and bringing huge economic benefits to the user.
Selection of commonly used metal cutting tools
Therefore, it is very important to deeply study and practice the knowledge of tool passivation. This subject should start from the following two aspects, one is to select the edge type and parameters, and the other is to explore the edge passivation technology and parameters to achieve a close combination of the two.
Edge shape and edge passivation shape
Common edge type:
Sharp edge: The edge of the knife sharpened before and after the sharpening, and it is naturally formed. The edge is sharp, with poor strength and easy to wear. Generally used for finishing tools.
Chamfering edge: On the rake face near the cutting edge, the edge sharpens the negative negative rake edge, which greatly improves the strength of the cutting edge. For roughing and semi-finishing tools.
Anti-sharpening edge: grinding a very narrow negative relief edge on the flank near the cutting edge, increasing the contact area between the tool and the workpiece during cutting, eliminating the vibration during the cutting process. Used for single-edged tools used when the process system is not rigid.
White blade: A narrow edge or land with a back angle of 0° is milled on the flank near the cutting edge, which can play the role of support guide and squeeze finishing. It is used for multi-edged tools such as reamers and broaches.
Rounding edge: Edge grinding or passivation into a certain parameter of the fillet on the counterpart, increase the edge strength, improve tool life, for a variety of roughing and semi-finishing tool can be indexed.
Cutting edge passivation geometric shape, has a great influence on the tool life: one is a circular arc-shaped edge, in the edge of the blade corner to form a symmetrical arc, accounting for more than 80% of the tool used for rough finishing. A kind of waterfall-type cutting edge, the ratio of the top surface to the side surface at the corner of the cutting edge is generally 2:1, which is an asymmetric arc and is suitable for harsh impact machining.
The tool cutting edge passivation technology aims at solving the defects of the micro-gap of the tool edge after sharpening as described above, so as to reduce or eliminate the frontal value, and achieve a smooth and smooth surface, which is both sturdy and durable. According to different processing conditions, a reasonable choice of cutting edge type and parameters, and tightly combined with the choice of counterpart passivation parameters, correctly handle the tool "sharp" and "solid" relationship, "sharp" is the tool cutting processing must have The characteristics, while considering the "solid" of the cutting edge, are also for the purpose of more effective machining, increasing the tool life and reducing the cost of the tool.
Manual passivation:
The earliest passivation tools began with leather and oil, such as shave at the barber shop, and barbers knifed on the leather to make the blades sharper and more durable. As for the tools used in machining, our predecessors had a lot of rich experience in boring knife, and the effect was very significant.
Examples are as follows:
During roughing, a new sharpened tool boring tool can reduce the wear value of the primary wear stage. In the later stage of the normal wear stage, the boring tool can still extend the normal wear stage. Generally, the tool life is increased by more than 0.5 times.
When the reamer is used for finishing, the internal hole surface of the boring tool may not reach the drawing requirements sometimes, and the surface roughness of the boring tool may be stable Ra1.6-0.8 祄, and the tool life may be increased by about 1 time.
The fine-grained machine tool guideway adopts a negative-angled wide-blade calendering knife. Its front and rear flank must be carefully ground through a flat plate. The surface quality can be improved to ensure that the cutting edge is straight and straight, and the surface roughness of the guide rail can be stabilized to Ra0.8祄 or less.
Mechanical passivation
In order to increase the passivation efficiency and quality, high-efficiency mechanical passivation methods are mostly used. Such as vibrating passivation, dielectric passivation, passivation of abrasives, rubber wheel passivation with abrasives, dry or wet sandblast passivation, roll passivation and passivation with abrasive nylon brushes.
According to the production and use certificate of the relevant manufacturer, the blade edge passivation machine meets the design requirements, the performance is reliable, and the blade edge passivation effect is good.
The selection of passivation parameters through the development of cutting blade passivation machine and production practices, preliminary grasp of some laws, for different processing conditions, select the edge type and passivation parameters is very important. Because of the different material of the blade and the different processing conditions, the selected cutting edge type and passivation parameters are also different, otherwise the expected effect of prolonging the tool life can not be achieved. Compared with the foreign blade passivation parameters, the 70% tool passivation value is between 0.0254-0.0762. Maximum: 0.127-0.2032mm. Minimum value: 1/6 of a 0.0762 mm hair strand, ie 0.0127 mm. Even if the passivation is so small, the tool edge is significantly strengthened.
The practice of passivation of a large number of counterparts has been verified: the edge is not necessarily sharper, and it is not necessarily the more blunt the better. It is best to determine different passivation values ​​for different processing conditions.
The combination of edge passivation and counterpart pattern is the most common and most effective measure to increase the strength of the counterpart and increase the tool life to reduce the tool cost.
Grinding the negative inverted nucleus with a microgrinding wheel has a small microscopic notch (up to 0.005-0.010 mm) and a small passivation parameter (0.010-0.030 mm), making the cutting edge sharp and durable. There is information that more foreign use.
The cutting edge passivation technology is still a problem that is not yet widely considered by people. It is important that the passivated tool can effectively improve the edge strength, improve tool life and the stability of the cutting process. We all know that the tool is the “teeth†of the machine tool, and the main factors that affect the cutting performance and tool life of the tool, in addition to the tool material, tool geometry parameters, tool structure, cutting amount optimization, etc., experience through a large number of tool edge passivation: A good edge pattern and edge passivation quality are also prerequisites for cutting tools faster and easier.
Metals, alloys and composite powders commonly used in thermal spray hardfacing technology and coating service. These unique powders are instantly heated by thermal spraying (welding) methods such as high temperature flame or explosive flame, and are sprayed and deposited on the cold or hot workpiece surface with high-speed heat flow in a molten or semi-melted state to form a surface Reinforcing layer, in order to improve the wear resistance, corrosion resistance, heat resistance, oxidation resistance or repair of external dimensions of the workpiece surface. XTC produces WC, CrC, Oxide Ceramic, Boride Powder, Metal Alloy Powder, Pure Metal and Spray Wire, etc. product. For HVOF/HVAF/plasma/Flame spray coating and applications. Meet the wear and corrosion resistance requirements of different surfaces.
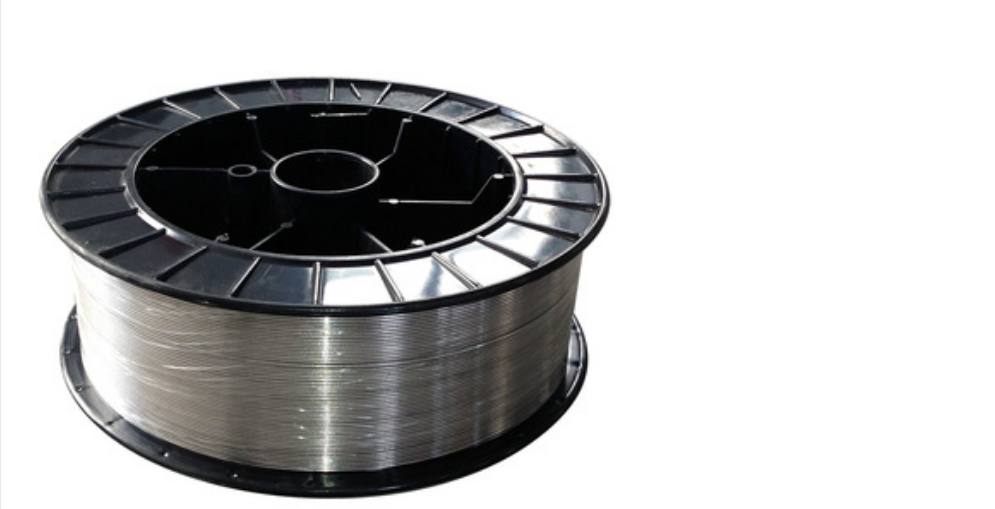
WC, CrC oxide ceramic powder and boride products are excellent in wear resistance and high temperature corrosion resistance. Taking WC products as an example, the hardness can reach HV1300-1500, and the temperature of CrC products can reach 800 degrees Celsius.
Metal alloy powder, Pure Metal and Spray Wire products have more applications in glass mold, steel and machinery industries. And XTC products are now become more and more popular in Metal spray coating and thermal spray coating industry.
Coating Service,Metal Spray Coating,Flame Spray Coating,Thermal Spray Coating
Luoyang Golden Egret Geotools Co., Ltd , https://www.xtccarbide.com