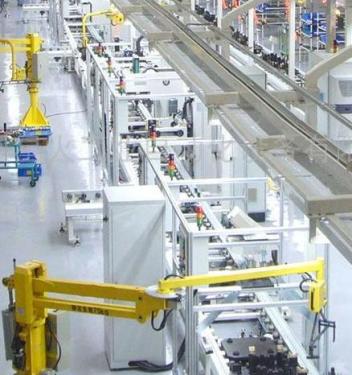
Conservatives in factory automation have also limited the establishment of wireless communication networks. Since cable can still be used, why should it be replaced with wireless? Having said that, there are more and more companies joining the ranks of wireless applications, and began to customize the robust wireless products in the factory environment. These companies improve the performance of their industrial networks by choosing the right infrastructure and wireless technologies. The drop in the price of wireless products also promotes companies to convert wired networks into wireless networks, or both. Especially in the current economic situation, the initial investment in wireless networks is lower than that of wired networks. For example, a sewage treatment plant that drowns water hundreds of meters away from the central control room and uses wireless networks to save a lot of money. Condition monitoring applications can also reduce component costs by using wireless networks. For example, slip rings used to monitor rotation functions do not need to be purchased under wireless conditions and can be replaced by a wireless sensor.
In summary, by 2013, the application of wireless communication systems in global factory automation will increase by about 40% annually. To some extent, the growth will be facilitated by automation component suppliers. They have gradually realized that wireless technology will be the foundation for the next technology to take off, greatly improving the efficiency of the factory and ensuring the safety of users. Now the question for machine builders and end users needs to consider is how to choose the application that is most suitable for wireless networks to get the maximum profit.
Facial Mask Packaging Bag Pouch,High Barrier 3 Side Sealed Cosmetic Mask Bag,Aluminum Foil Cosmetic Facial Mask Sachet,Cosmetic Face Mask Packaging Bag Pouch
Shenzhen Lehua Packaging Materials Co., Ltd , https://www.shenzhenlehua.com