I. Introduction
A press brake is a machine tool used in metal forming to bend and shape metal sheets. These machines are widely utilized in industries such as construction, automobile, aerospace, and others involved in sheet metal processing and manufacturing.
The workpieces produced by a press brake can have various shapes, ranging from simple to complex parts. The press brake is equipped with various pressure systems, including mechanical, hydraulic, electric, and pneumatic.
The power device exerts pressure on the ram, causing the upper die to move downwards and press the metal plate into the lower die, thereby completing the sheet metal bending process. Through repeated and precise bending operations, the desired workpiece is produced.
The press brake's die is comprised of two parts: the upper die (punch) and the lower die. The combination of these two dies, with their different shapes, acts upon the plate to form workpieces of various shapes.
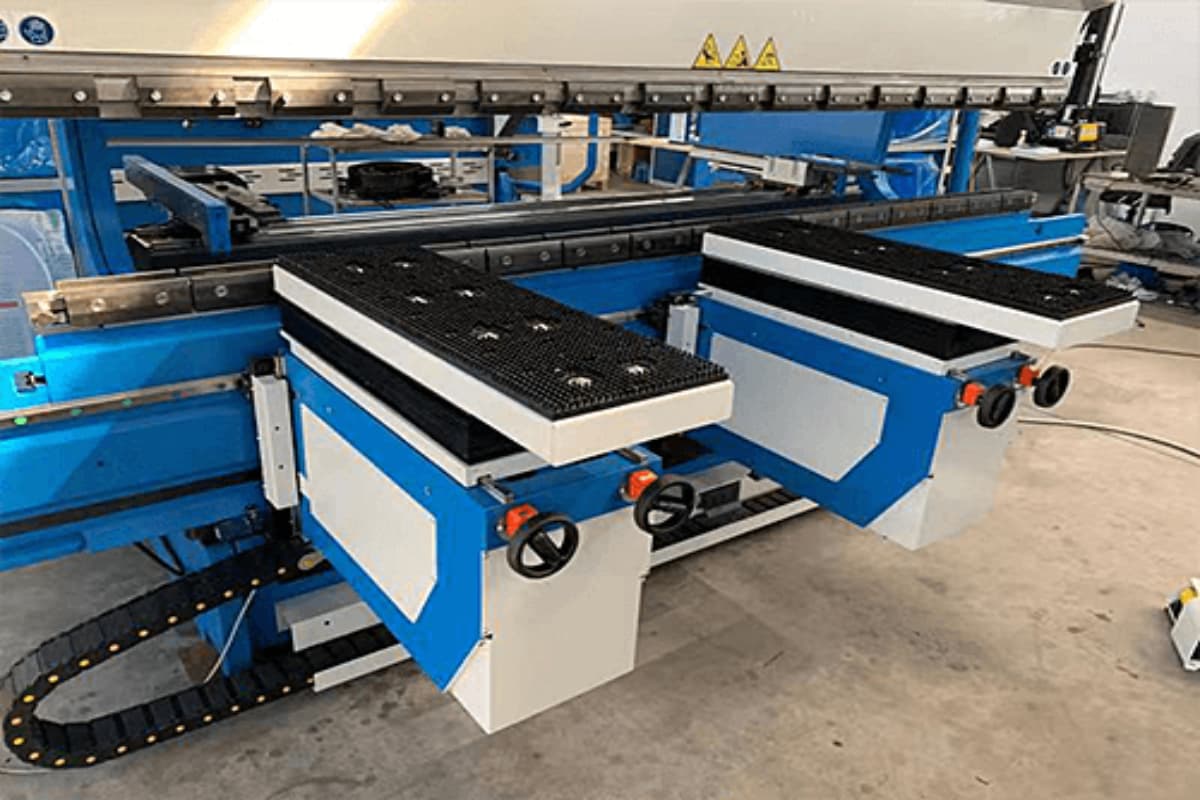
II. Overview of Press Brake Tools and Accessories
1. Different Types of Press Brake Tools and Their Functions
The components of a press brake include a conventional die assembly, an upper die (punch), and a V-shaped die. It is important to choose different press brake dies based on the type of metal sheet being used.
For instance, when working with metal plates that have high tensile strength, the die must also have a matching hardness to prevent damage to the die or incorrect bending of the metal sheet.
The conventional tooling group consists of an upper die and a lower die, which work together to bend the metal sheet. The punch is usually made of materials with high hardness to effectively extrude or cut the metal plates.
Similarly, the lower die requires a material of equal hardness since the punch will press the metal sheet into it. The upper die (punch) of the press brake can have special shapes and angles to produce workpieces with specific shapes.
These special punches include standard punches, gooseneck punches, sash punches, arrow punches, acute punches, and others.
Press brake dies are commonly made from hardened steel, such as chromium-molybdenum steel, to prevent punch cracking caused by excessive pressure or plate hardness. The use of materials with high hardness also helps ensure the durability of the punch.
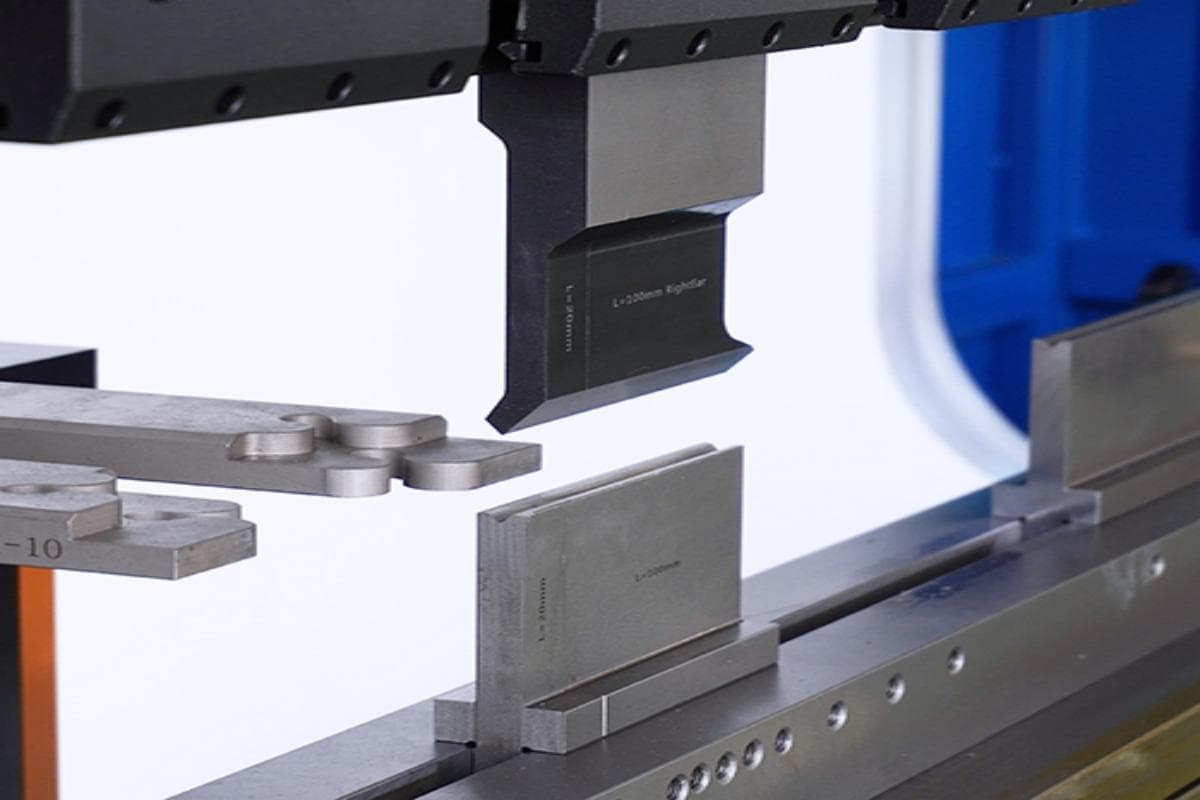
The lower die of a press brake can be classified into four types: the V-shaped die, the U-shaped die, the single die, and the double die. The V-shaped and U-shaped dies are made of the same material as the punch and are known for their durability and high hardness.
The size of the opening in the V-shaped die affects the choice of bending radius for the workpiece and the method of bending. The lower die's groove is designed to fit the upper die, allowing the sheet to be securely fixed and molded into the final shape of the workpiece.
Punches and dies are the primary tools for press brake. In addition to these, the universal press brake also has other essential special press brake tools such as the back gauge, clamping tool, and support rack.
Other components of the press brake work together to ensure accurate bending position, angle, and speed, resulting in improved accuracy and quality of the final workpiece, increased productivity, and reduces operator fatigue.
2. Using High-Quality Press Brakes Bending Tools and Accessories
The significance of using high-quality press brake punches dies, and accessories are obvious. These components can improve the precision of parts by providing precise press brake dies and other accessories.
The punch and die material should be sturdy enough to withstand wear and breakage. Quality tooling materials can also extend the lifespan of the tool and prevent deformation.
High-quality tooling ensures the quality of the bent workpiece, reducing errors in the final product. This, in turn, improves press brake production efficiency and reduces production costs.
Dies with a high level of matching and quality are highly effective in sheet bending. Advanced and high-quality accessories can enhance bending speed, accuracy, and final product quality.
For instance, accurate positioning of the backgauge and each axis can enhance the accuracy of the flange length and size of the workpiece. Quality hydraulic devices can provide consistent stroke and eliminate bending angles caused by inconsistent speed.
By using high-quality tooling and accessories, the bending quality of the press brake is ensured and the machine's lifespan is extended. This results in guaranteed product quality, improved production efficiency, and reduced production costs.
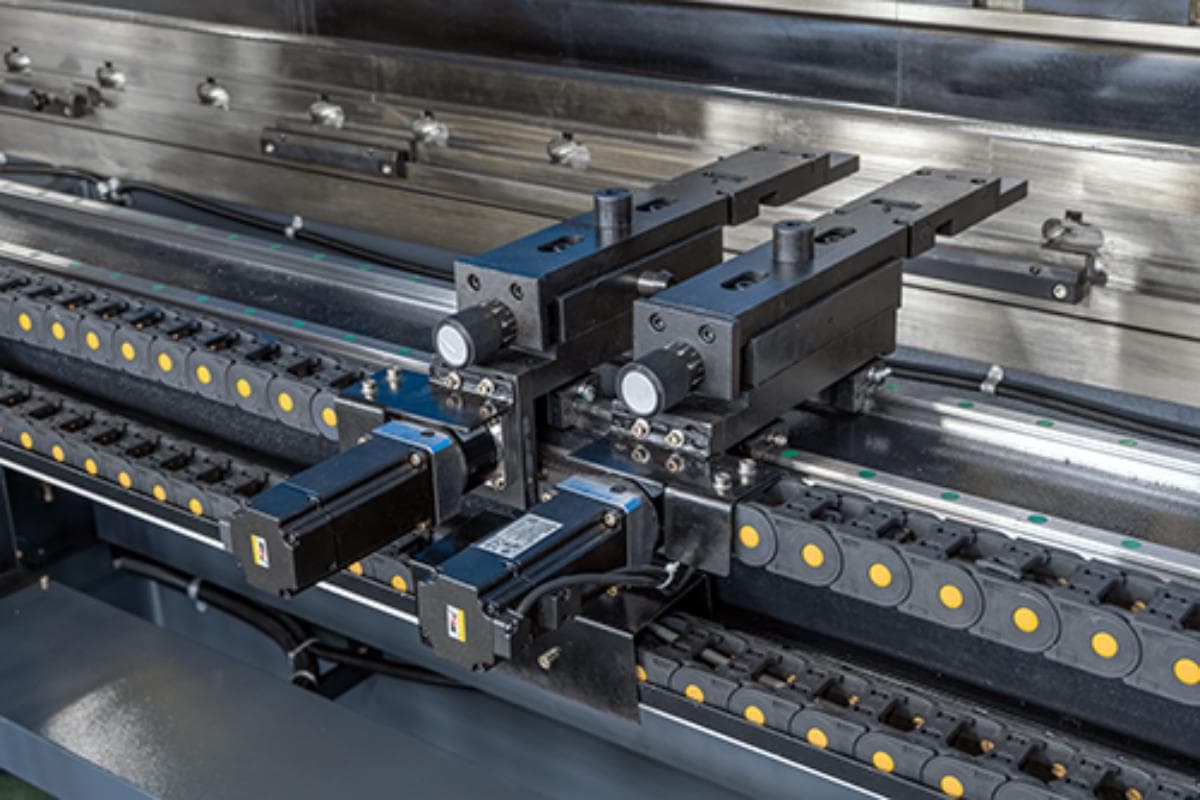
III. Common Press Brake Tools and Accessories
1. Press Brake Dies and Punches
The press brake die is divided into two parts, the upper die and the lower die, which work together to bend the sheet metal. The upper die can be further divided into various types of bending dies such as right angle, acute angle, obtuse angle, gooseneck die, standard die, and others.
The lower die, on the other hand, consists of different types such as the V-shaped die, U-shaped dies, single groove die, and double groove die. The upper die, powered by the ram, presses the metal sheet into the lower die, shaping it into the desired form. The die is typically made of high-hardness steel to prevent breakage.
Here is the detailed information on the specifications of different types of punch tools and die tools used in press brake operations:
Punches
Type | Dimensions (mm) | Material | Hardness (HRC) | Suitable Metal Thickness (mm) | Remarks |
Standard Punch | 835x130x26 | 42CrMo4 | 52-58 | 0.5-6 | Commonly used for 90°bending, weight 12kg |
Acute Angle Punch | 835x97x26 | 42CrMo4 | 47±3 | 0.5-6 | Suitable for acute angle bending, weight 10.5kg |
Gooseneck Punch | 835x120x56 | 42CrMo4 | 47±3 | 6-12 | Avoids workpiece interference, weight 13kg |
Radius Punch | 835x145x32 | 42CrMo4 | 47±3 | 6-12 | Used for radius bending, weight 13.3kg |
Z-Shape Punch | 835x197x92 | 42CrMo4 | 47±3 | 12-20 | Used for Z-shape bending, weight 15kg |
Dies
Type | Dimensions (mm) | Material | Hardness (HRC) | Suitable Metal Thickness (mm) | Remarks |
Single V Die | 835x116x26 | 42CrMo4 | 47±3 | 0.5-6 | Commonly used for right-angle bending, weight 13kg |
Double V Die | 835x97x26 | 42CrMo4 | 47±3 | 0.5-6 | Suitable for multi-angle bending, weight 10.5kg |
Multi V Die | 835x120x56 | 42CrMo4 | 47±3 | 6-12 | Multiple V-groove sizes, weight 13kg |
U-Shape Die | 835x145x32 | 42CrMo4 | 47±3 | 6-12 | Used for U-shape bending, weight 13.3kg |
Four-Way Die | 835x197x92 | 42CrMo4 | 47±3 | 12-20 | Four different groove sizes, weight 15kg |
- Material: 42CrMo4 is a high-strength alloy steel known for its excellent mechanical properties and wear resistance.
- Hardness: The hardness of 42CrMo4 typically ranges from 47 to 58 HRC, depending on the heat treatment process.
- Suitable Metal Thickness: The design of punches and dies is suitable for different thicknesses of metal sheets, typically ranging from 0.5mm to 20mm.
- Dimensions: Standard lengths are 835mm, with segmented lengths of 415mm available to fit different workbench sizes.
- Weight: The weight of different types of tools ranges from 10.5kg to 15kg, depending on the size and design of the tool.
2. Angle Gauges and Protractors for Measuring Bend Angles
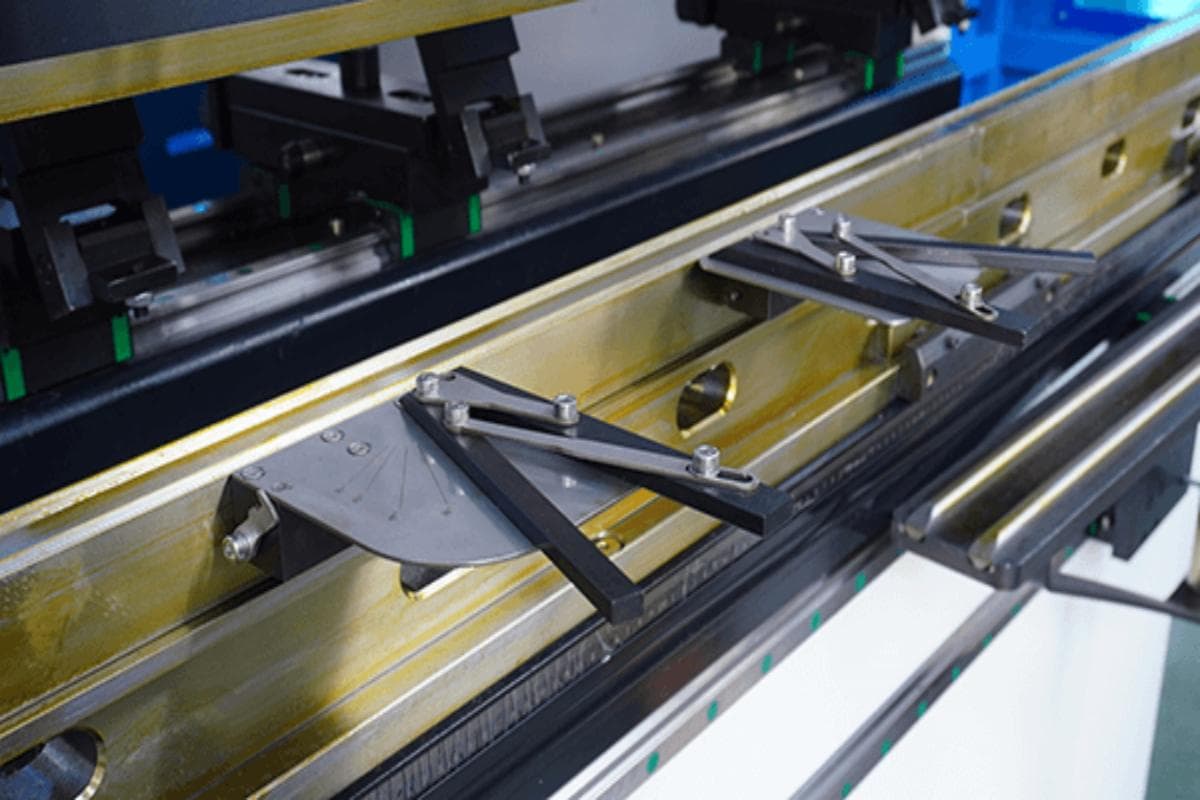
When bending metal plates, the tools used to measure the bending angle are referred to as angle gauges and protractor. Press brake punches and dies are used to shape the metal sheets into various angles and forms.
To guarantee the precision of the bending angle, angle gauges, and protractors can be employed. Correct the bending angle and verify its accuracy by using the angle gauges and protractor. There are various kinds of angle gauges and protractors, typically made of steel for support.
3. Press Brake Tools Lubrication
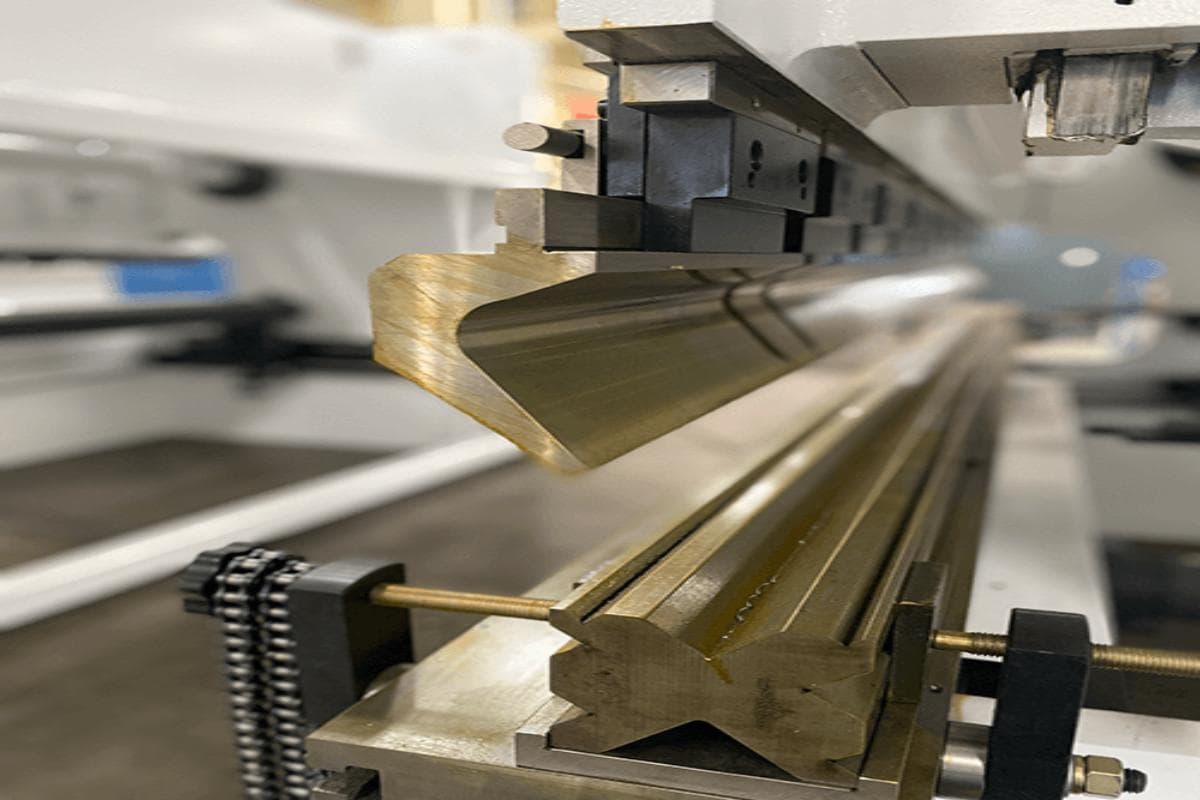
The utilization of lubricants can reduce wear and tear caused by long-term use of the press brake dies and components. The lubricants used for the press brake consist of cutting oil, grease, and wax. Lubricants can enhance the bending efficiency and prolong the lifespan of the press brake.
4. Safety Protection Devices
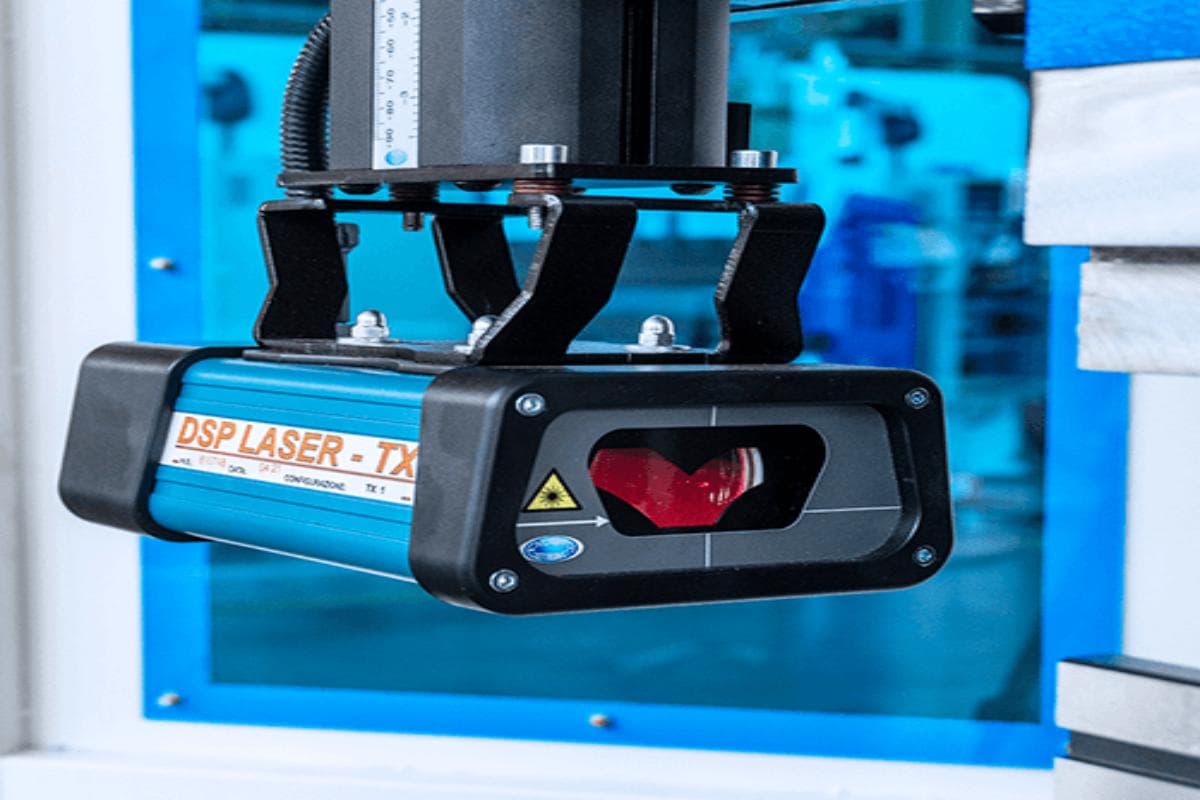
To protect the operator from any harm during bending, the press brake must be equipped with safety and protective devices. Such safety protection devices include protective fences, gloves, and other personal protective equipment.
Additionally, there are specialized protective devices installed on the press brake's operating parts. The press brake's brake caliper is fitted with a guard plate, which acts as a thermal braking component. Contact with this component may result in injury to the operator.
IV. Conclusion
This blog aims to introduce you to the common press brake tools and highlight the importance of using high-quality tools in metal fabrication. The wide range of press brake tooling used in a press brake machine includes press brake punches and dies, a backgauge, a protractor, a hydraulic device, and a protective device, among others.
High-quality press brake tools are an essential component of a top-performing press brake machine. In the long run, choosing a press brake with a moderate price but high quality can effectively reduce production costs.
ADH specializes in press brake dies and press brake manufacturing and boasts high quality, exceptional performance, and a cost-effective price. If you require further information about the ADH press brake, please contact us to assist you.
Taizhou Yuansheng Stainless Steel Products Co., Ltd. , https://www.ss-wirerope.com