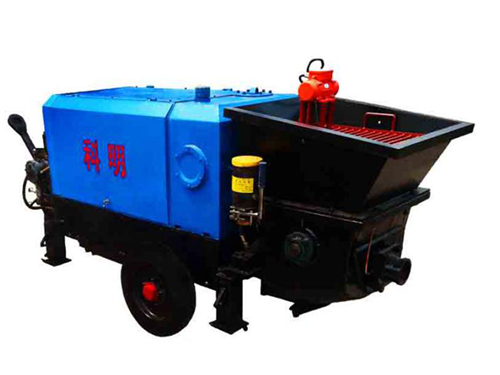
Some environmental experts pointed out that most of the dust in the air now comes from construction sites. (Respirable particulate matter is dust and it is in most cases the primary pollutant of air quality.) Building dust is the main source of dust. Especially in recent years, the construction of cities around the country has been accelerating, and the number of large and small projects across the country has led to an increase in the proportion of building dust, accounting for the bulk of all types of dust, and the number has risen. Seriously affect the quality of the local air and endanger our healthy life.
What harm do dust have on the human body?
1, the local effect, that is, on the skin, cornea, mucous membranes and other local stimuli, resulting in a series of lesions.
2, poisoning effect, that is, inhalation of toxic dust, can be dissolved in the bronchial and alveolar wall after absorption, causing poisoning.
Occupational respiratory diseases, including pneumoconiosis, dust deposition, and respiratory cancer.
According to statistics, the use of cement in construction dust and its associated total dust emissions account for 35% of the total amount of construction dust. It can be said that the dust emission during cement use is the main source of pollution for construction dust. So how to solve the cement pollution in construction? Today Xiao Bian gave us a brief introduction of the dust spray equipment commonly used on 3 construction sites.
KSP series wet sprayer
KSP-9 concrete wet sprayer is mainly used in iron (public) tunnel engineering. The equipment is easy to operate, low dust, less rebound, protection of the environment, and improve the quality of the spray layer, a special vibration hopper so that the concrete can smoothly enter the batching system, the standard metering pump can accurately add accelerator, low pressure and low speed vortex flow delivery, The working principle of short-distance injection overcomes problems such as blockage, pulse, segregation, etc. The spray stream is even and stable. Improve spray material.
KBS-8A Pumped Wet Sprayer
Performance characteristics
1. High work efficiency: Adopting full hydraulic pumping design, system reliability can be greatly improved.
2, spray distance: the maximum level of 200 meters, 80 meters vertically. (4 times the jet distance of traditional equipment)
3, the injection volume is continuously adjustable. (continuously variable speed)
4. The amount of quick-setting agent added can be adjusted within the scope of 0 to 9%.
5. Low consumption of equipment accessories: The service life of main wearing parts is not lower than 3000m3 (It is 10 times of the service life of the wearing parts of rotary piston wet spray machine)
6, centralized lubrication system, effectively extending the life of wear parts.
7. The product wheel design is small and flexible, easy to move and easy to maintain.
8, the transport of small aggregate concrete, high-rise building mortar delivery.
9, heat insulation lightweight foam cement, mortar to warm, self-leveling ground construction.
10. Jetting of plain concrete and fiber concrete in various projects.
11, fire, insulation material injection (delivery).
12. The injection (transportation) of greening soil in the construction of ecological environment.
13. Pressure perfusion of various types of foundation piles, tunnel over-digging and backfilling, railway slope support, and disaster management.
KCPZ dust sprayer
Performance characteristics:
1. Having two inventions and utility model patents, the machine body and nozzles break the traditional limitations
2. The latest type of environmentally-friendly concrete injection equipment reduces dust by more than 90% compared with conventional jets, reducing environmental pollution and fully protecting the physical and mental health of construction workers.
3, the new nozzle device, mixing more evenly, rebound greatly reduced.
Innovation:
1, the upper and lower overflow and rotor friction plate leakage collection and export devices to prevent dust emissions.
2. The new dust removal technology and filter material have good filtering effect and long service life.
3, drawer type ash container, easy to clean.
4, multi-ring water sprinkler system to ensure uniform mixing.
Sheet metal forming processes are those in which force is applied to a piece of sheet metal to modify its geometry rather than remove any material. The applied force stresses the metal beyond its yield strength, causing the material to plastically deform, but not to fail. By doing so, the sheet can be bent or stretched into a variety of complex shapes. Sheet metal forming processes include the following:
l Bending
l Roll forming
l Deep Drawing
l Stretch forming
Bending
Bending is a metal forming process in which a force is applied to a piece of sheet metal, causing it to bend at an angle and form the desired shape. A bending operation causes deformation along one axis, but a sequence of several different operations can be performed to create a complex part. Bent parts can be quite small, such as a bracket, such as a large enclosure or chassis.
V bending and Wipe bending
Roll forming
Roll forming, is a metal forming process in which sheet metal is progressively shaped through a series of bending operations. The process is performed on a roll forming line. Each station has a roller, referred to as a roller die, positioned on both sides of the sheet. The shape and size of the roller die may be unique to that station, or several identical roller dies may be used in different positions. The roller dies may be above and below the sheet, along the sides, at an angle, etc. the roller dies are lubricated to reduce friction between the die and the sheet, thus reducing the tool wear. Also, lubricant can allow for a higher production rate, which will also depend on the material thickness, number of roll stations, and radius of each bend. The roll forming line can also include other Sheet Metal Fabrication operations before or after the roll forming, such as punching or shearing.
Deep drawing
Deep drawing is a metal forming process in which sheet metal is stretched into the desired part shape. A tool pushes downward on the sheet metal, forcing it into a die cavity in the shape of the desired part. The tensile forces applied to the sheet cause it to plastically deform into a cup-shaped part. Deep drawn parts are characterized by a depth equal to more than half of the diameter of the part. These parts can have a variety of cross sections with straight, tapered, or even curved walls, but cylindrical or rectangular parts are most common. Deep drawing is most effective with ductile metals, such as aluminum, brass, copper, and mild steel. Examples of parts formed with deep drawing include automotive bodies and fuel tanks, cans, cups, kitchen sinks, and pots and pans
Stretch Forming
Stretch forming is a metal forming process in which a piece of sheet metal is stretched and bent simultaneously over a die in order to form large contoured parts. Stretch forming is performed on a stretch press, in which a piece of sheet metal is securely gripped along its edges by gripping jaws. The gripping jaws are each attached to a carriage that is pulled by pneumatic or hydraulic force to stretch the sheet. The tooling used in this process is a stretch form block, called a form die, which is a solid contoured piece against which the sheet metal will be pressed. The most common stretch presses are oriented vertically, in which the form die rests on a press table that can be raised into the sheet by a hydraulic ram. As the form die is driven into the sheet, which is gripped tightly at its edges, the tensile forces increase and the sheet plastically deforms into a new shape. Horizontal stretch presses mount the form die sideways on a stationary press table, while the gripping jaws pull the sheet horizontally around the form die
Sheet Metal Forming,Sheet Metal Forming Services,Custom Sheet Metal Forming,Precision Sheet Metal Forming
Suzhou FCE precision electronics Co., LTD , https://www.sjfukeyifcesz.com