The 2 cigarette lighter sockets (DC outlets) provide a total power of up to 150W, perfect for simultaneously use of multiple car appliances
  Dual USB Charging Ports ,enable you to charge 2 devices simultaneously. The 1A port is ideal for charging iPhones, Android cell phones, MP3 players, etc. The 2.1A port can quickly charge your iPads and other tablets.
 High Safety Standards
  Designed with anti-corrosion metal connectors, heavy duty copper wires and protective circuits prevent your devices from overloading or overheating.
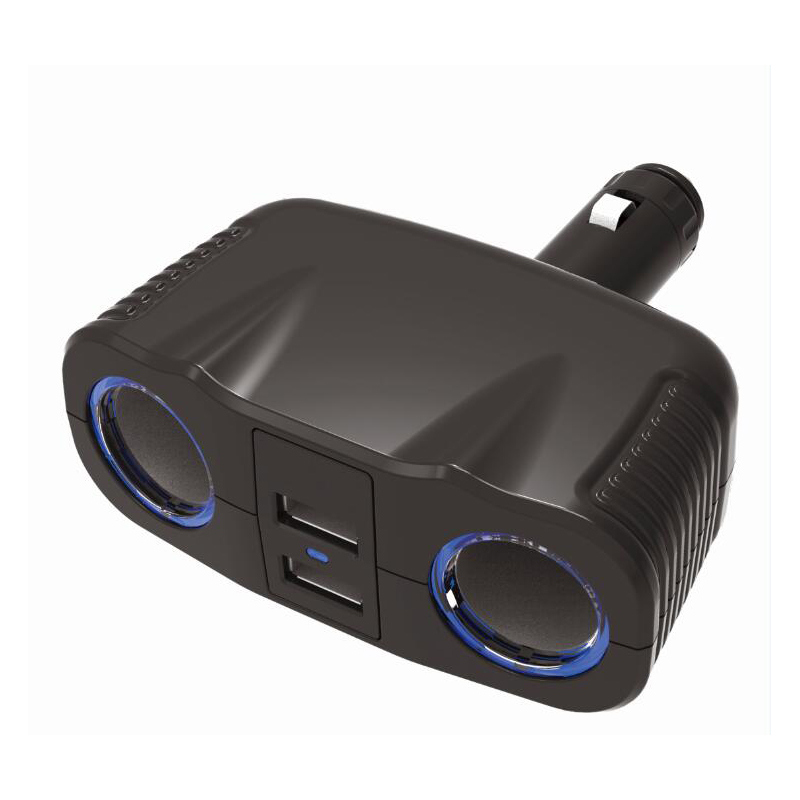
Product Specification
• Rated Power (2 DC Socket): 150W
• Input Voltage: 12V / 24V DC
• Output Voltage: 12V / 24V DC
• Dual USB Output: 5V DC/3.1A in totalOur Services
Our Services
1. Reply your enquiry in 24 working hours
2. Experienced staffs answer all your questions in fluent English
3.Customized design is available .
4.Exclusive and unique solution can be provided to our customer by our well-trained and professional and staffs
5. Special discount and protection of sales area provided to our distributor.
Company Information
Since the foundation in 1995, our company has been dealing in the line of auto electric appliances and auto accessories for more than 10Â
years with customers worldwide and established close friendship and cooperation with them.
Our factory, located in Hangzhou, close to Shanghai, covers an area of more than 200,000 square feet while the building area is aboutÂ
140,000 square feet. We have 12 assembly lines in the factory and also an injection molding plant with 20 injection machines.Â
Our products are mainly in the line of auto accessories, such as Car Fan, Car Vacuum, Car Jump Start, Car Air pump, Car Air Compressor,Â
Car worklight and etc. For the good quality and pleasing design of our products, we have a ready market in both America and Europe, and
 have connections with some of the largest retail stores and distributors in the world. With the rapid development of our company these
 years, we sincerely want to cooperate with customers from all over the world on the basis of mutual benefits.
Why Choose Tonny
1.20 years experience in producing auto battery chargers.
2.Our products listed by CE,RoHS,CETL and other authority certifications
3.Experienced staff and worker assure superior product quality
4.Advanced quality management system
5.Strong technology research and development abilityÂ
 Our working parter
1.   We are supplier of Walmart and WALGERRNS ,LIDL ,CVS ,HOMEDEPOT ,ACADEMY ,MEIJER ,VDI ,LOME"S,
TARGET ,O2COOL ,SCOTTS .........
2.  Expertise.  We are professional manufacturer with rich experience in manufacturing Car vehichle chargers smart phone chargers
and USB data cables.
3.   Quality Assurance.  Professional product line. well-trained workers,strict QC standard and 10years focus on OEM ITEMS
4.   Good Service.  Customer is the God,aim to provide the best service for you ,with a competitive and GOOD quality,and on thime
delivery .12months warranty for all productsÂ
  The 2 cigarette lighter sockets (DC outlets) provide a total power of up to 150W, perfect for simultaneously use of multiple car appliances
  Dual USB Charging Ports ,enable you to charge 2 devices simultaneously. The 1A port is ideal for charging iPhones, Android cell phones, MP3 players, etc. The 2.1A port can quickly charge your iPads and other tablets.
 High Safety Standards
  Designed with anti-corrosion metal connectors, heavy duty copper wires and protective circuits prevent your devices from overloading or overheating.
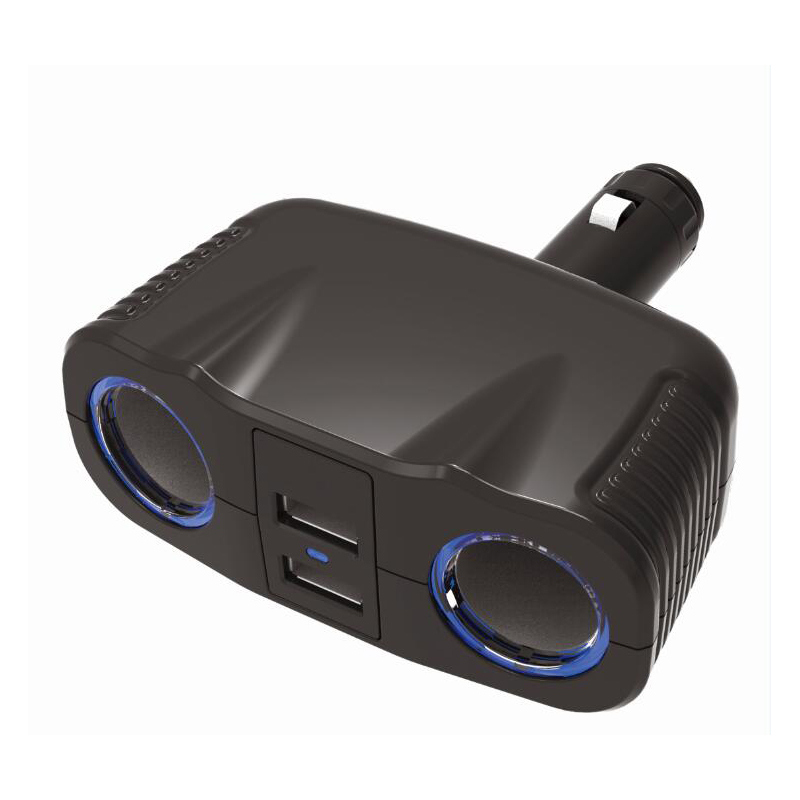
Product Specification
• Rated Power (2 DC Socket): 150W
• Input Voltage: 12V / 24V DC
• Output Voltage: 12V / 24V DC
• Dual USB Output: 5V DC/3.1A in totalOur Services
Our Services
1. Reply your enquiry in 24 working hours
2. Experienced staffs answer all your questions in fluent English
3.Customized design is available .
4.Exclusive and unique solution can be provided to our customer by our well-trained and professional and staffs
5. Special discount and protection of sales area provided to our distributor.
Company Information
Since the foundation in 1995, our company has been dealing in the line of auto electric appliances and auto accessories for more than 10Â
years with customers worldwide and established close friendship and cooperation with them.
Our factory, located in Hangzhou, close to Shanghai, covers an area of more than 200,000 square feet while the building area is aboutÂ
140,000 square feet. We have 12 assembly lines in the factory and also an injection molding plant with 20 injection machines.Â
Our products are mainly in the line of auto accessories, such as Car Fan, Car Vacuum, Car Jump Start, Car Air pump, Car Air Compressor,Â
Car worklight and etc. For the good quality and pleasing design of our products, we have a ready market in both America and Europe, and
 have connections with some of the largest retail stores and distributors in the world. With the rapid development of our company these
 years, we sincerely want to cooperate with customers from all over the world on the basis of mutual benefits.
Why Choose Tonny
1.20 years experience in producing auto battery chargers.
2.Our products listed by CE,RoHS,CETL and other authority certifications
3.Experienced staff and worker assure superior product quality
4.Advanced quality management system
5.Strong technology research and development abilityÂ
 Our working parter
1.   We are supplier of Walmart and WALGERRNS ,LIDL ,CVS ,HOMEDEPOT ,ACADEMY ,MEIJER ,VDI ,LOME"S,
TARGET ,O2COOL ,SCOTTS .........
2.  Expertise.  We are professional manufacturer with rich experience in manufacturing Car vehichle chargers smart phone chargers
and USB data cables.
3.   Quality Assurance.  Professional product line. well-trained workers,strict QC standard and 10years focus on OEM ITEMS
4.   Good Service.  Customer is the God,aim to provide the best service for you ,with a competitive and GOOD quality,and on thime
delivery .12months warranty for all productsÂ
Although there are many welding jobs which are best handled manually, and many more that can be done manually if necessary (as, for example, if a welding operation is too small to have an automatic welding machine, or if repairs must be carried out far from one of these devices), there are also many welds that can be handled quite adequately by an automated welding process. Some, such as pipe welding in the case of large pipes in many industrial applications (such as oil drilling platforms and chemical factories, to name only two examples), must be handled by an automatic welding machine such as an orbital welder, because of the precision that needed to avoid springing a potentially hazardous leak.
There are two different situations where an automatic welding machine is typically used. Semi-automatic welding uses a pre-programmed automatic welding machine, but the parts are actually loaded onto the welding bench (or its equivalent) by an operator, who arranges them and then switches on the welding machine until the weld has been completed. The operator then removes the finished workpiece and repeats the process as many times as necessary.
Fully automatic welding removes the human element except as an overall observer to make sure the machines are running properly. In these set-ups, the parts and finished workpieces are moved by other machines, such as conveyer belts, and the welding operation is often continuous over a large number of individual pieces. This is a truly industrial use of the automatic welding machine, and is found mostly in very large operations such as car factories.
Automatic welding machine benefits and drawbacks
Automatic Welding Machines have both their advantages and disadvantages, and as is the case with so many things, a gain in one place is compensated for by a loss in another. Automatic welding machines are much faster than skillful human welders can ever hope to be, and produce decent workmanship despite their greater speed. An automatic welder is roughly eight times faster than a manual welder. These welders do not pause or tire, although they may eventually become overheated and need to be shut down for a time. Since a lot of welding scrap is generated by welder fatigue when a human is wielding the electrode, there will be less wastage over the course of a long work day when automatic welding systems are the main `workers.`
Automatic welding machines also provide a high quality weld, since they are totally uniform in their application of the electric arc or other welding tool. The machines are always on the job, unless they happen to break down, and once they have been purchased, they do not need to be paid.
Conversely, human welders still retain a few advantages over automatic welding machines. The cost of setting up even a modest array of automatic welders can be in area of a quarter million U.S. dollars, so the initial outlay on a human welder is much smaller. Automatic welders also take an extremely long time to set up, so the urgency of the welding job also needs to be weighed in the balance. Manual welding is extremely flexible, while automatic welding machines carry out the task in a repetitive manner and must be completely reconfigured if a different weld needs to be made. Also, if maintenance is not handled properly, the machines may break down and cause a disastrous pause in production. Automatic welding machines are fast, efficient, and highly useful, but they are not a complete solution to every situation and this must be borne in mind by their potential users.
Full or Semi Automatic welding systems come in many shapes and sizes and can be used for a variety of applications from welding pipe to ship building.
Column & Boom (TIG, Plasma, MIG & Submerged Arc Process)...
To meet the stringent requirements of aerospace and nuclear related applications column and boom manipulators need to provide exceptional rigidity and low deflection under load. Other important requirements include smoothness and consistency of axis movement. In meeting these demands a range of column and boom manipulators have been designed featuring high quality sub components and stress relieved fabrications that are incorporated into a design, which provides class-leading stability. This design philosophy is carried through to larger heavy-duty models.
Light duty and standard range generally have more applicability to Aerospace and light precision engineering applications, where minimal boom deflection and lack of vibration at full boom extension are important factors. Options exist for precision boom drive (for linear welding applications) or even precision column drive (vertical) utilizing recirculating ball screw type mechanisms. As for all column and boom manipulators both boom and column motions can be via precision bearings and guide ways. Design features include thick section fabrications that have been stress relieved to ensure highest standards of straightness and dimensional tolerance. Applicable weld processes include TIG, plasma and MIG/MAG, where high level weld head payload is not a primary factor.
Heavy Duty and Extra Heavy Duty column and boom manipulators share the same design features common to the light and standard duty manipulators so they also can be used for precision applications involving processes such as Dual Arc – Plasma / TIG. However, these units will find application mainly involving MIG/MAG and submerged arc (SAW) processes offer a range of optional extras including powered carts and king pin rotation of the column. Special oversized travel carts are available to carry all control and weld process equipment.
If factory space is an important consideration then we can offer models which feature telescoping of the boom, thus minimizing space requirements to the rear. Movement of the telescoping sections is synchronous to ensure the highest possible smoothness of motion is maintained.
All Column and boom manipulators are designed to work with a range of controls. Depending on size and duty, boom motion control may be via a frequency inverter type drive with encoder feedback.
Brands of Column and Boom welders include Bode, ESAB, SAF, Lincoln, Gullco, Pandjiris, Ransome, Arsonson
Seam Welders (TIG, Plasma & MIG Process)...
Longitudinal seam welding systems accommodate manufacture of tubes and pipes for a very wide range of material thickness and length. Applications range from the seam welding of small diameter tubes with short length and ultra thin wall thickness for bellows and instrument manufacture, through to large diameter beverage and brewing tanks, and thick wall pressure vessels.
Brands of Seam welders include Bode, Jetline, Pro-Arc, SAF, AMET, ESAB, Koike
Seam Welding Industry Examples...
Below are some examples of advanced seam welding technologies being used in a variety of commercial sectors - Aerospace, Automatic, Bellows, Fume Extraction, Water Heating Tanks, Dairy machinery
seam weldingseam welding automotiveseam welding bellowsseam welding fume extractionseam welding water heating tanksseam welding water heater tanks
Welding Lathes (TIG Plasma and MIG Process)...
Supplied are used Lathe type circumferential welding systems to suit small components such as bellows, sensors and transducers, right through to a diverse range of larger components including, hot water tanks, fuel containers, nuclear waste containment, food and beverage containers.
For small to medium size components we offer our New Pro-Arc lathe range. These head and tailstock units feature ultra low backlash harmonic type gearboxes and encoder servo motor drive. Options exist for bench and freestanding models featuring controls suited to the most demanding precision application. Typical weld processes include Micro TIG, Micro plasma, TIG, Plasma and MIG.
Circumferential lathe type welding systems can accommodate components with diameters up to 1500mm and weights up to 10,000Kgs. Smaller models are ideal for welding components such as Air Cylinders, Valve Assemblies, Catalytic Converters and Hydraulic Actuators. Various control options are possible including PLC, Typically welding process selection would be TIG, plasma and MIG reflecting thicker section weld requirements.
Brands of lathe welding equipment include Bode, Jetline, Pandjiris, Pro-Arc, Weldlogic,
Welding Lathes Industry Examples...
Below are some examples of advanced welding lathe technologies being used in a variety of commercial sectors.
Aerospace Technical Welding, Instrument and Transducers, Steam, Air and Water Pressure Welding, Welding of Munitions
Robotic Welding Equipment
There are two popular types of industrial welding robots. The two are articulating robots and rectilinear robots. Robotics control the movement of a rotating wrist in space. A description of some of these welding robots are described below:
Rectilinear robots move in line in any of three axes (X, Y, Z). In addition to linear movement of the robot along axes there is a wrist attached to the robot to allow rotational movement. This creates a robotic working zone that is box shaped.
Articulating robots employ arms and rotating joints. These robots move like a human arm with a rotating wrist at the end. This creates an irregularly shaped robotic working zone.
There are many factors that need to be considered when setting up a robotic welding facility. Robotic welding needs to be engineered differently than manual welding.
A robotic welding system may perform more repeat ably than a manual welder because of the monotony of the task. However, robots may necessitate regular recalibration or reprogramming.
Robots should have the number of axes necessary to permit the proper range of motion. The robot arm should be able to approach the work from multiple angles.
Robotic welding systems are able to operate continuously, provided appropriate maintenance procedures are adhered to. Continuous production line interruptions can be minimized with proper robotic system design. Planning for the following contingencies needs to be completed:
· Rapid substitution of the inoperable robots.
· Installing backup robots in the production line
· Redistributing the welding of broken robots to functioning robots close by
Brands of Robotic welders include Motoman, OTC, Kuka, ABB, Fanuc, Panasonic, Miller, Lincoln
Benefits of robotic welding
Productivity
A robot typically works between two or more work stations. This means that during the robot welding cycle the operator is unloading a welded assembly and then loads new components to a welding fixture. Because there is less handling compared to a manual weld cycle the robot achieves much higher levels of arc-on time. The robot also moves very quickly between the joints and this yields a further saving in cycle time. Typically a robot system will increase output by a factor of two to four. This depends on the nature of welding. An assembly with lots of short welds can be produced with the most time savings. The cost savings that robot welding brings, can help companies to be more competitive and beat off competition from low cost manufacturing countries in Eastern Europe or China. In order to assess what sort of productivity improvements can be achieved it would be appropriate to compare manual welding times with robot welding times.
Quality
The robot has a very high repeatable accuracy (± 0.08 mm) and excellent path following accuracy. The robot presents the welding gun at the correct welding angle, welding speed and distance. The high level of integration to the welding equipment ensures that optimum welding conditions can be used for each and every joint. The end result is consistent high quality output, day in day out, year in year with reduced cost for rework, scrap or removal of weld splatter.
Consumable costs
It is up to the judgment of a manual welder to weld to the correct standard, but often the weld is oversize. A robot however, always welds to the correct length and size of weld that it has been programmed to produce. This means that some potential savings in wire consumption can be made. If for example a manual welder welds a 5 mm fillet, where only a 4 mm fillet is required, the savings in welding wire alone will be a staggering 36%!
Labour
In recent years it has become increasingly difficult to employ manual welders. There tends to be a certain amount of staff turnover and this of course carries a cost for recruitment and training. When labour is an issue companies often find themselves working overtime or having to employ additional contract labour to meet demands and this can have a serious impact on production costs. If products cannot be supplied to the end customer, penalties may be incurred or future business may be at risk. Whilst there will always be a requirement for manual welding, companies that invest in robotic automation are much less dependent on manual welding.
Safety
A robot welding system addresses health and safety issues associated with dangerous welding fumes and exposure to arc-flash. Companies can reduce the risk of their employees claiming compensation if they are affected by the hazardous working environment.
Flexibility
The robot can be used to weld many different products and allows companies to consider Just In Time production. By reducing work in progress and stock levels, savings can be made due to fact that less value is added to stock levels in terms of labour, transport and storage costs.
Floor space
Compared to the same output from manual welding bays the robot requires less floor space.
Automatic Welding And Cutting Equipment
Automatic Welding And Cutting Equipment,Automatic Pvc Welding And Cutting Equipment,Automatic High Frequency Welding Equipment,Automatic High Frequency Cutting Equipment
Changzhou Edaweld Trading Company Limited , https://www.edaweld.com